Dust Control
The escape of airborne dust from bulk material handling systems is a hazardous and costly problem.
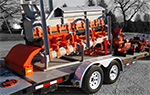
Jimmy Cable
Product Field Display Specialist
8 years with Martin
How you might
interact with Jimmy:
Jimmy drives the Martin® Road Show Demo Trailer all over the country, to site visits, tradeshows, etc.,
Favorite thing about Martin:
The company itself. Martin is family-oriented and every employee - from the newest, entry-level position to the highest management - operates as "Team Martin."
Favorite thing about driving the demo trailer:
Meeting new people in different regions. The demo trailer allows me to promote Martin, its services, and its products.
Something I want
customers to know:
I truly take pride in meeting and greeting customers. Demonstrating Martin's products shows the world Martin's credibility, professionalism, and dedication to one mission.....Problem Solved!
Orlando Utilities
Problems Addressed:
Dust, Spillage, Safety
Orlando Utilities Commission – Stanton Energy Center (SEC)... wanted to increase the safety aspect by limiting dust and spillage from one of its principal conveyors, engineers wanted to reduce airborne particles and eliminate a potential source of trips and falls. They also wanted to reduce clean-up and maintenance time, allowing critical manpower to be utilized elsewhere and improve plant efficiency. Additionally, preventing coal dust spillage would help minimize wear on rollers and other moving components, saving on replacement part costs and labor.
Continue reading...
Wellness Walks
Martin Engineering encourages a healthy & active lifestyle for its employees. This month's featured activity is Wellness Walks. All participants are rewarded with Wellness Tokens that can be spent on several wellness-approved items.
|
Gary Swearingen
Product Specialist - Dust Control
31 years industry experience
FACT OR FICTION: FOAM & DUST CONTROL
Fiction: Once the foam system is installed and operating, it will control the dust without needing many adjustments.
Fact:
While those operating a foam system might not have this false expectation, it is important to understand that in order to maintain good-quality foam, routine adjustments are required. Water quality, water pressure, and air pressure all affect the quality of the foam at the application point, and need to be monitored and adjusted.
Fiction:
You can see the foam being added to the material stream, ensuring the application is effective.
Fact:
While you may be able to see the foam being applied to the material stream, this does not ensure proper dust control. The proper application of a surfactant requires adequate mixing with the material. If the foam can be seen resting on top of the cargo, it has not been mixed into the material and the effectiveness of the foam should be questioned. There is a difference between applying foam to see foam and applying foam to control dust.
Fiction:
As much as 3% moisture must be added to the material stream to control dust.
Fact:
Surfactant blends have been developed to achieve effective results with minimal moisture addition. Surfactants are used to treat the water supply to increase the ability of dust particles to become attached to water droplets. Having a good surfactant that is applied at the right pressure and flow is critical. How and where to spray are also key to reducing moisture addition and increasing efficiency. Knowing what to spray on a particular application is the science, knowing how to spray is the art to a successful application.
For more information, contact Gary at 800-544-2947 extension 324.
F4 refers to Foundations™ 4 - the 4th edition of Martin's book on improving belt conveyors and controlling fugitive material. We will break up the book into short, easy-to-read articles for your convenience.
LINEAR VIBRATORS
Linear vibrators activate the material inside a chute or bin by using heavy blows on the outside of the structure’s steel walls.
Hammering on the bin or chutewall leads to damage to the wall surface, often called "hammer rash."
Linear vibrators activate the material inside a chute or bin by using heavy blows on the outside of the structure’s steel walls. In fact, the earliest form of vibration was a hammer. The act of pounding on the chute or bin wall overcomes the adhesive force between the material and the wall surface. However, this hammering on the bin or chutewall often leads to damage to the wall surface. The marks left on the wall by the hammer, often called "hammer rash," will continue and expand the problem the blow of the hammer was supposed to overcome. In addition, the swinging of the sledgehammer poses the risk of injuries to plant personnel. The piston vibrator was developed to produce this effect without actually swinging a hammer.
Download full article
CleanScrape Belt Cleaner
New Belt Cleaner Pays For Itself
- Extremely Long Life
- Minimal Maintenance
- Tungsten Carbide Tips
- Safe For Mechanical Splices
Download our calculator to see your savings
What do YOU want to read?
|