Products Used | ApronSeal™ Double Skirting , Impact Cradle LD , Martin® External Wear Liner , Roller Tracker™ |
---|---|
Product Types Used | Belt Cleaning Solutions , Transfer Point Solutions , Belt Alignment , Belt Sealing , Belt Support |
Industry | Power Generation |
Customer | Kolin Thermal Power Plant |
Problem
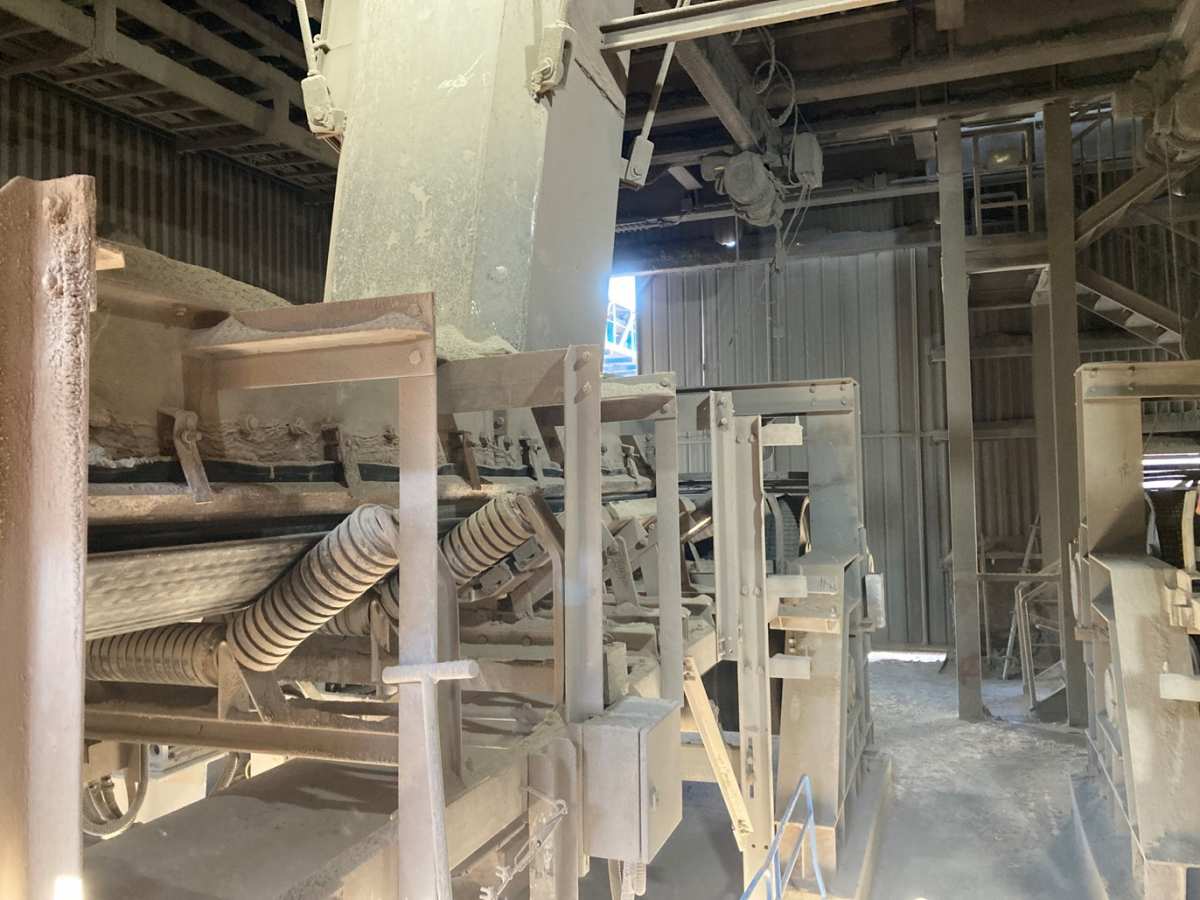
Soma Kolin Thermal Power Plant, located in the Soma district of Manisa province, has been operational since 2019 with a capacity of 510 MW, using local lignite fuel. The 1100 mm wide PC05-A conveyor system, which transports ash at temperatures of 80º-100ºC was causing dust and spillage problems. Insufficient sealing and belt support in the material feed area have led to spillage and excessive dusting. Additionally, the primary and secondary scrapers used in the conveyor's discharge area were not been able to provide adequate cleaning, leading to spillage problems on the return path. This situation has posed serious concerns for both safety and efficiency.
Solution
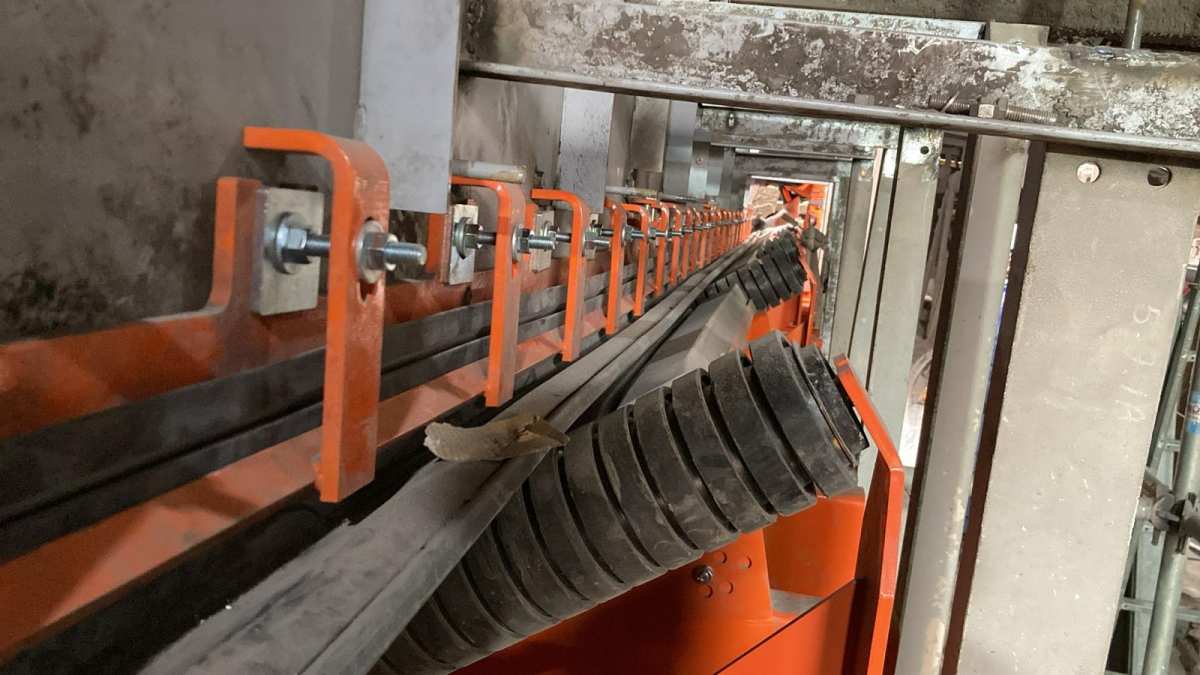
Martin Engineering Turkey experts thoroughly analyzed the situation and developed a quick solution plan. At the transfer point, the loading chute, which had insufficient capacity, was redesigned to a 7.5-meter length. Martin Service Technicians installed a Martin® Impact Bar, three Side Support Bars, five Track Mount Impact Roller Stations, Double ApronSeal™ Sealing Rubber, Wear Plates, Roller Tracker belt centering device, and Torsion V-Plow Plus Tail Scraper.The impact bar and side support bar system, instead of rollers, consists of low-friction, energy-absorbing bars that support the belt. This system helps reduce dusting by supporting the side skirts. In the discharge area, QC1 XHD Primary Scraper and Orion 2000 Secondary Scraper were installed to prevent spillage issues on the return path of the conveyor. These solutions are designed to eliminate dust and spillage problems, thereby improving efficiency and ensuring safety.
Result
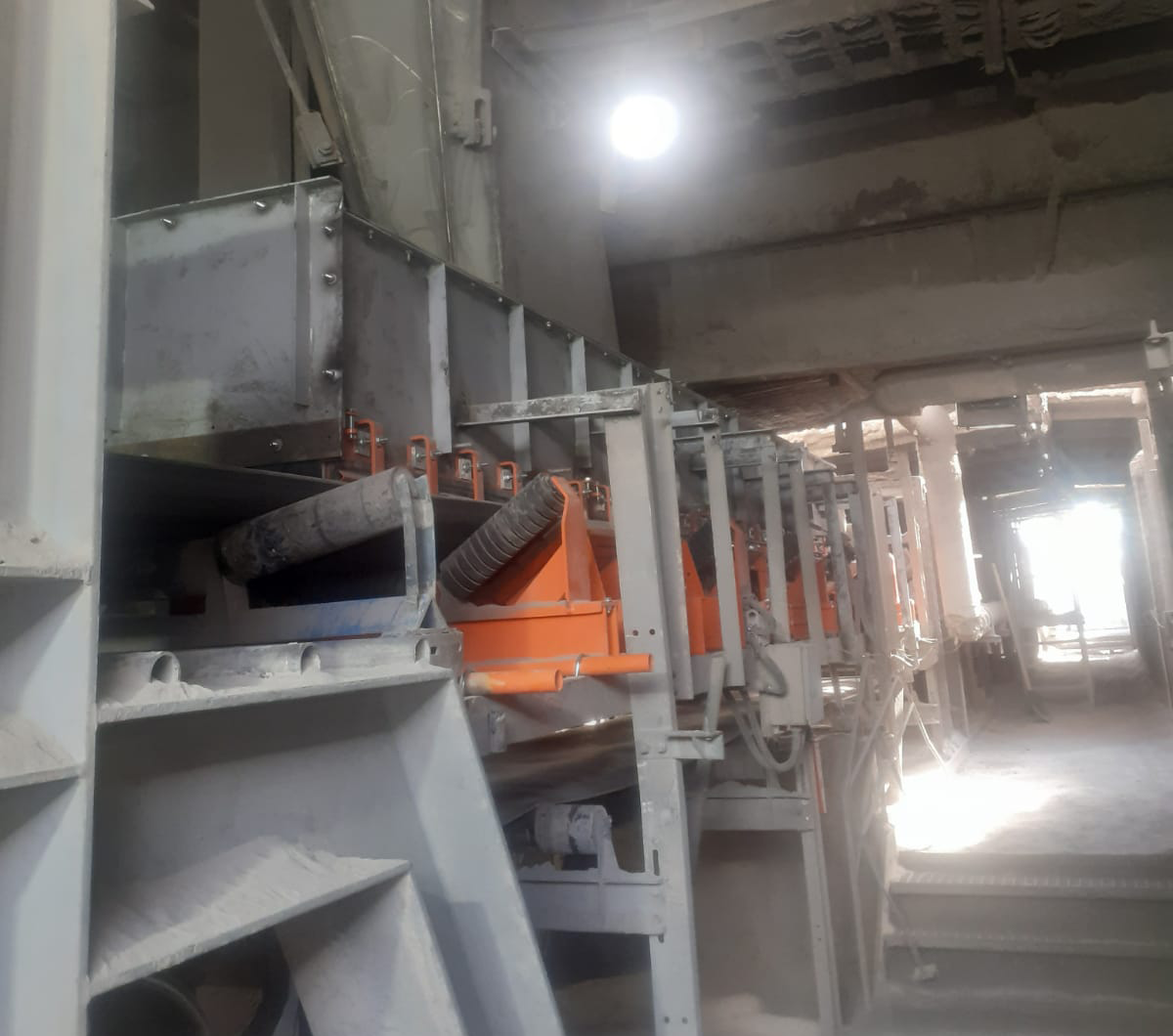
Thanks to the redesigned loading chute and the installed systems, the dust level in the environment has decreased by 80%. The difference before and after the implementation is visibly significant. These improvements have made the conveyor belt cleaner safer, and more efficient. The need for manual cleaning on the belt has been eliminated, reducing safety risks and freeing up labor for other tasks, thus increasing production efficiency.Belt Capacity: At Soma Kolin Thermal Power Plant, approximately 1,000 tons of ash are transported daily (daily capacity). Due to the improvements made, dusting on the belt has decreased by 80%, which equates to approximately 800 kg of dust reduction per day.Labor Savings: Previously, each shift resulted in a labor loss of approximately 1-2 hours for manual cleaning. By eliminating this need, approximately 2-4 hours of labor per day have been saved. This time has been redirected to other operational areas.The customer is very satisfied with these improvements and plans to implement this reference project on other belts within their budget. This will help achieve overall efficiency increases and safety improvements across the entire plant.